Inhaling tiny particles of crystalline silica can cause irreversible lung scarring, difficulty in breathing, permanent disability, lung cancer, kidney damage and auto immune disease.
Cutting, grinding, drilling, oiling or polishing engineered stone as well as other materials containing crystalline silica, generates tiny particles of crystalline silica dust which enter the atmosphere and can enter a worker’s airways.
Employers have an obligation to protect their workers from this potentially fatal dust found in many workplace environments, such as:
- Stone cutting and installation of the stone used in kitchens, bathrooms, laundries and landscaping
- Mining
- Quarrying
- Tunnelling
- Construction
- Glass, pottery and ceramic manufacturing
- Brick and tile manufacturing
- Sand blasting
- Abrasives manufacturing
- Slate works
- Foundries
When will symptoms develop?
Jobfit’s National Medical Director, Dr Ilse-Marie Stockhoff says the severity of a crystalline silica related condition and the time it takes for symptoms to appear will vary from person to person and will depend on the level of exposure.
“There are many variables that determine the way crystalline silica affects workers,” Dr Stockhoff said.
“These include the duration and severity of exposure, the silica content in the material they are working with and what effective control measures are in place.
“Given the wide variance of these factors, all work involving crystalline silica should be treated as high risk,” Dr Stockhoff said.
Dr Stockhoff says that the silica / quartz content varies in different materials (see table) but most dangerous is the dust generated by processes involving manufactured stone (also known as engineered stone or artificial stone).
“These man-made products can contain up to 95% silica,” said Dr Stockhoff.
“There are some calls to ban manufactured or engineered stone due to the extremely high level of crystalline silica they contain”
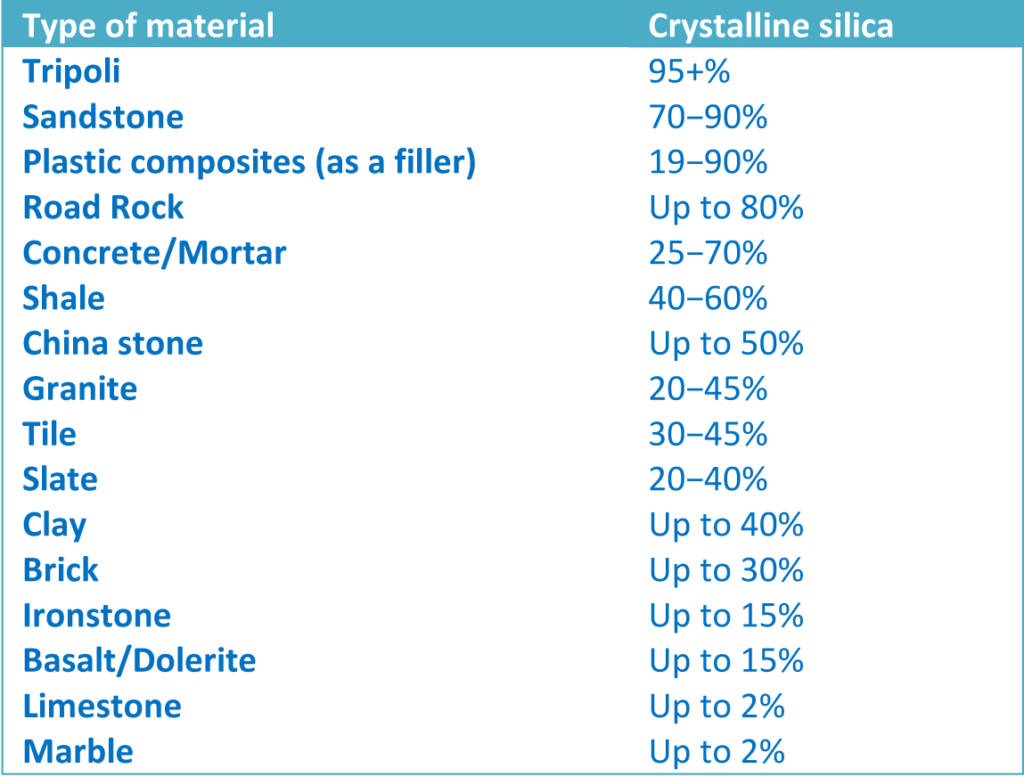
Types of materials and average silica content
How can employers control exposure to Crystalline Silica dust?
Ideally, the risk of exposure to crystalline silica should be eliminated. But this isn’t always practical.
Instead, employers must ensure appropriate risk control measures are carried out to protect workers from exposure to crystalline silica as far as reasonably practical. Dr Stockhoff says these should include:
Risk Assessment
Identify high risk processes and locations through hygiene surveys. In addition, assess workplace exposure to crystalline silica dust to ensure it remains below the current Occupational Exposure Limit (OEL) of 0.05mg/m3 averaged over an 8-hour work day.
Elimination
Use material that does not contain crystalline silica.
Substitution
Use a different product with lower amounts of crystalline silica such as natural stone.
Isolation
Use automated, fully enclosed and contained machines to cut, grind or polish material containing silica stone slabs.
Engineering Controls
Minimise exposure through effective engineering controls and work practices such as:
- On-tool water suppression (wet methods)
- On-tool dust extraction, e.g. dust class M or H vacuum cleaner
Personal Protective Equipment (PPE)
Employers must provide and ensure proper use of Respiratory Protective Equipment (RPE) by all workers exposed to crystalline silica dust, at all times (not just when engineering controls cannot adequately control the dust). Furthermore:
- The RPE must comply with AS/NZS 1716: respiratory protective devices and should be at minimum a P2 filter
- Consideration should be given to half-face negative respiratory or powered air-purifying respirator (PAPR) in high-risk environments
- Respiratory fit testing is recommended to ensure adequate fit and efficacy of protection
Training & Education
For example, Tool Box Talks which provide information, instruction, training and supervision.
Medical Assessment / Health Surveillance
Employers must provide and fund an initial or baseline medical assessment, and ongoing periodic medical assessments to exposed workers.
Which workers should be protected?
It’s not just the workers ‘on the tools’ who should be considered in crystalline silica workplaces.
All roles, both on and off-site should be risk assessed and appropriately supported. These may include workers involved in:
- Storage
- Transport
- Handling
- Cleaning and using tools containing crystalline silica
- Cleaning and maintenance of workspaces where crystalline silica is used
How Jobfit can help you meet your Crystalline Silica requirements
Jobfit’s highly experienced clinical staff are available to assist with specific employer crystalline silica related requirements. We can provide:
- Toolbox talks by our experienced clinical staff
- Initial or baseline health assessment: for any worker who commences work with crystalline silica for the very first time or is a new employee to an employer, but not necessarily new to crystalline silica work
- Periodic health assessments: a requirement for every worker who is already working with and exposed to crystalline silica dust at their existing employer. Employers are responsible for all costs involved during a Health Assessment and this may include referrals for additional investigations, e.g. HRCT or Complex Lung Function
- Respirator fit testing
Contact our team today to find out how we can assist with your crystalline silica requirements.
Do you know the requirements in your jurisdiction?
As an employer, it’s important to stay up to date with the obligations relevant to your state, territory or governing body in regard to crystalline silica in the workplace and protecting workers from deadly dust. At this time, requirements are outlined below including Safework Australia criteria and guidelines.
Queensland
RSHQ Coal Mine criteria for Coal Mine Workers
- 5 yearly health assessments with spirometry unless the supervising doctor indicates the need for more frequent assessments
- 5 yearly ILO CXR with 2 NIOSH B-reader reports
RSHQ Mineral Mines and Quarries criteria for Mineral Mines and Quarry Workers
- 5 yearly Health Assessments with spirometry unless the supervising doctor indicates the need for more frequent assessments
- 5 yearly ILO CXR with dual NIOSH B-reader reports
All other workers exposed to crystalline silica not including Engineered Stone Workers
Safework Australia criteria and guidelines:
- 3-5 yearly full health surveillance assessments which includes ILO CXR and report, preferably by a NIOSH B-reader
- Annual spirometry assessments
Engineered Stone Workers
- Annual health assessment with spirometry
- Periodic imaging will depend on results of previous medical assessment, ongoing level of exposure and clinical judgement
NSW
Order 43 Coal Services criteria
- 3 yearly health assessments
- ILO CXR with NIOSH B-Reader report every 3 years, unless clinically required for more frequent assessments
All other workers exposed to crystalline silica, not including Engineered Stone Workers
Safework Australia criteria and guidelines:
- 3-5 yearly full health surveillance assessments which includes ILO CXR and report, preferably by a NIOSH B-reader
- Annual spirometry assessments
Engineered Stone Workers
- Annual health assessment with spirometry
- Periodic imaging will depend on results of previous medical assessment, ongoing level of exposure and clinical judgement
SA/ VIC / NT / TAS
All workers exposed to crystalline silica, not including Engineered Stone workers
Safework Australia criteria and guidelines:
- 3-5 yearly full health surveillance assessments which includes ILO CXR and report, preferably by a NIOSH B-Reader
- Annual spirometry assessments
Engineered Stone Workers
- Annual health assessment with spirometry
- Periodic imaging will depend on results of previous medical assessment, ongoing level of exposure and clinical judgement
WA
Category A workers (Engineered Stone workers)
- Annual health surveillance and spirometry
- 2 yearly LDCT unless clinically required for more frequent assessments
Category B workers Miscellaneous (natural stone)
- Annual health surveillance and spirometry
- 5 yearly LDCT unless clinically required for more frequent assessments
Please refer to state and territory government websites for the most up-to-date regulations for your jurisdiction.